At SATO Group, our engagement with customers does not end when we deliver a product or implement a solution. We have a global support system in place to troubleshoot problems and offer suggestions for improvements to help users keep operations running stably with the SATO products/solutions they have deployed.
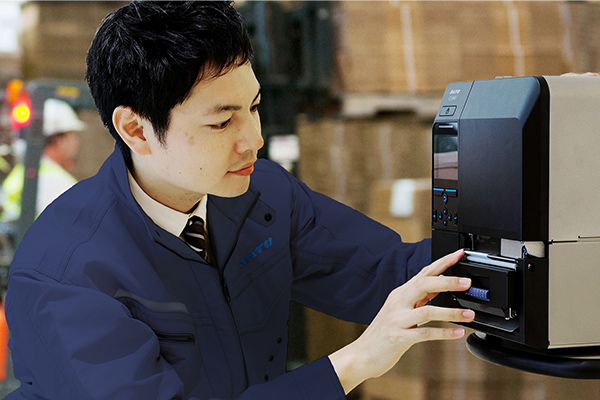
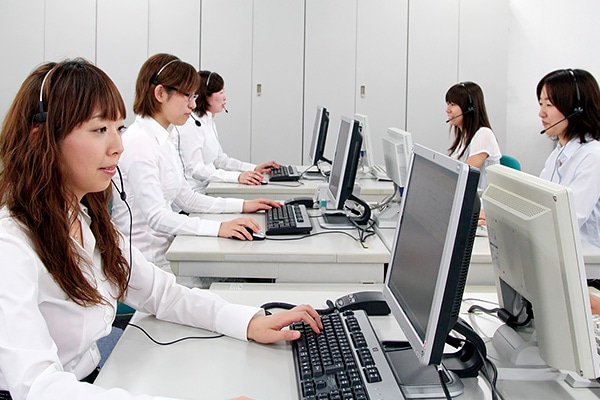
Providing after-sales follow-up around the world
When customers need support, they can call or email our help desk that works to provide assistance promptly. In Japan, we have a countrywide network for servicing and repairs to cover a wide range of hardware including SATO printers, data capture devices (e.g., barcode readers, handheld terminals) and magnetic card readers/writers in the event they malfunction or break down. Customers can choose to either have our customer engineers visit their worksites from about 40 support centers all over Japan or return their equipment to our eight maintenance centers for more extensive repairs.
Outside Japan, our sales offices in the Americas, Europe, Asia, and Oceania have dedicated technical teams that are capable of performing repairs and handling different issues reported by customers via both on-site and send-back services. Some of these teams collaborate with external business partners to ensure our customers enjoy peace of mind with seamless support no matter where they are operating from. Efforts are also being made to enable the tracking of technical faults/failures beyond borders and the periodic sharing of information related to new hardware/software products and maintenance so that we continue to strengthen our customer support system.
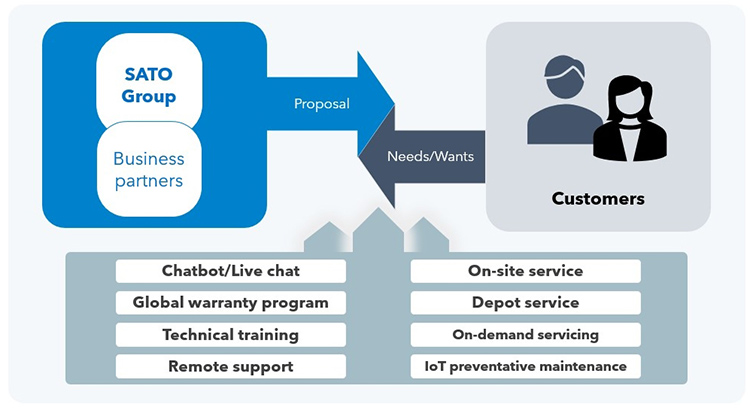
Comprehensive troubleshooting
We believe isolating the cause is the first step to solving problems with label printing processes or systems. To get to the root of a problem, we take the all-around approach of investigating not only our own printers but also the accompanying data capture devices, software, network/communication infrastructure, and consumables deployed in all aspects possible. Being a manufacturer of both printers and consumables, we know how to match printers with the right label materials, which is crucial for the successful troubleshooting of issues related to print speed or quality. As such, we can make sure that we are thorough yet detail-oriented at the same time in offering one-stop technical support to customers.
Taking maintenance services to the next level with IoT
For manufacturing and logistics sites, the sudden breakdown of label printers can put a halt to operations and have a major effect on the supply chain. To ensure stable operations, we have sought to diversify our lineup of maintenance plans* to include year-round and night-time support while also looking at new technologies that would improve our standard of service. In 2015, we launched SOS (SATO Online Services), an IoT-based maintenance service that is compatible with most new SATO printers. Being the world’s first IoT label printer service of its kind, SOS is capable of remotely monitoring printers at customer sites 24/7 and enabling preventative maintenance before issues become critical, which eliminates unplanned downtime. With the permission of users, data such as printer status and conditions of expendable parts that is automatically logged in the system is analyzed to help better the user experience.
*Maintenance plans vary depending on country and region.
Fostering professional technical talent
We put in place training programs for our technical personnel to pursue professional development, giving them the initiative to improve their own expertise and skills in line with the requirements of their respective countries and regions. Many countries in Asia, for example, are starting to adopt the model used in Japan which defines the technical training process by five essential aspects and appoints staff to the different ranks of Specialist, Expert, or Master, based on their achievement in each aspect. By setting clear expectations for work competencies and providing on-the-job coaching together with continuous feedback through performance evaluations, we hope to groom our technical personnel into professional talents with leadership qualities.
Example: Training program in Asia
1. Basic knowledge | Be proficient with maintenance/service agreements and procedures, and other technical knowledge related to mechanics, electronics, software, communication networks, and consumables. |
---|---|
2. Work quality | Display competency in the job by proposing effective solutions and working productively. |
3. Practical skills | Meet speed requirements for routine servicing tasks, resolve technical difficulties adequately, and clear other tests in practical assessments. |
4. Qualifications | Upgrade oneself continuously by acquiring various professional certifications in domains such as auto-ID technologies, information security management, industrial robotics, and IT. |
5. Team building | Develop/implement specific measures to increase team efficiency and produce results. |