At SATO, we are serious about employees maintaining physical and mental health and working safely. We hold regular Safety & Health Committee meetings consisting of representatives from different departments to check safety of workplaces and take preventive measures against work-related incidents.
Managing occupational safety and health in Japan
Central Safety & Health Committee
We take measures to keep employees safe and healthy by preventing work-related incidents, improving work conditions and creating conducive workplaces.
We have a central committee that manages occupational safety and health in Japan under the direction of our Executive Officers Meeting.
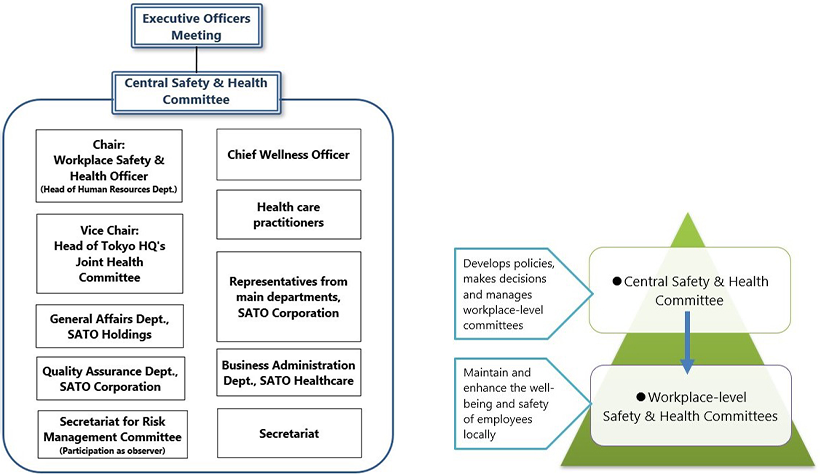
Workplace-level Safety & Health Committees
We have formed Safety & Health Committees or Health Committees at 24 branches/offices in Japan.
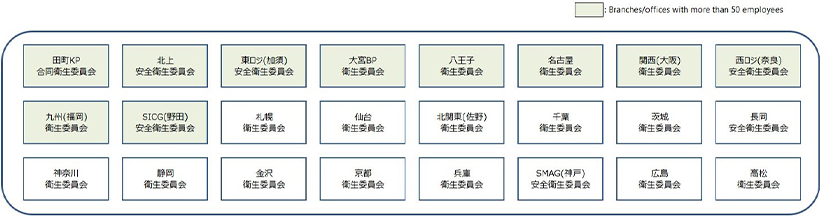
Workplace incidents reported in Japan
You can scroll through this table.
FY 2020 | FY 2021 | FY 2022 | FY 2023 | |
---|---|---|---|---|
Number of injuries or individuals injured | 11 | 7 | 10 | 14 |
Total lost workdays | - | 0 | 27 | 81.5 |
Lost time injury frequency rate | - | 0 | 0.8667 | 0.98471 |
Severity rate | - | 0 | 0.00498 | 0.01982 |
Installation of life-saving devices
We have installed AEDs (automated external defibrillators) at sales and servicing branches/offices in different parts of Japan.
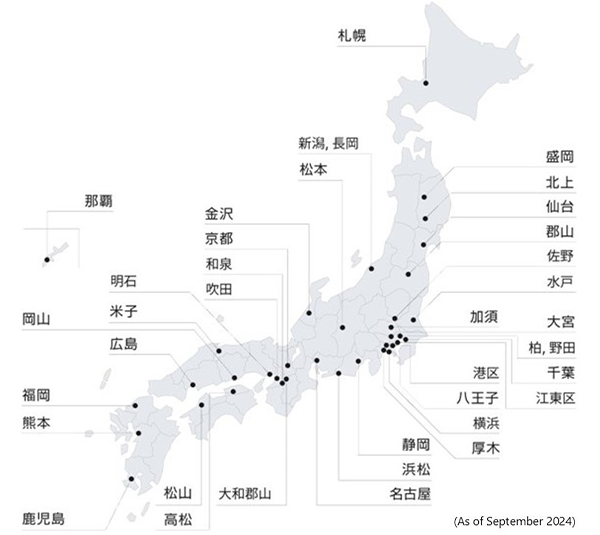
Occupational safety at hardware factories
In our printer/hardware factories in Malaysia and Vietnam, we follow our occupational safety and hygiene policy in maintaining and improving the workplace for the safety of all employees.
Our occupational safety and hygiene policy
We provide and maintain a safe and hygienic working environment for our employees, and protect people from risks that may arise from our activities. The management team and employees shall discuss and cooperate with each other to achieve the objectives below.
- Protect employees and others from injuries or illnesses owing to workplace-related factors.
- Provide employees information, instruction, training and supervision that are necessary to safe execution of work and related to health risks.
- Investigate the cause of any accident, dangerous occurrence or occupational poisoning/disease, and take actions to ensure that they never occur again.
- Comply with laws related to safety and health, as well as with guidelines and codes of conduct.
- Continue improving our control on safety and health, and revise this Policy whenever necessary.
We establish a safety and hygiene committee and appoint a safety and hygiene officer to ensure that the objectives of this policy are fully met and maintained.
Preventing work-related accidents
Our occupational safety and hygiene committee leads our daily actions to prevent incidents at work.
Monthly internal audits
Monthly in-house audits identify risks and renew our awareness of safety in the workplace. Any matters found in the audit as needing improvement are addressed in top priority and taken immediate action.
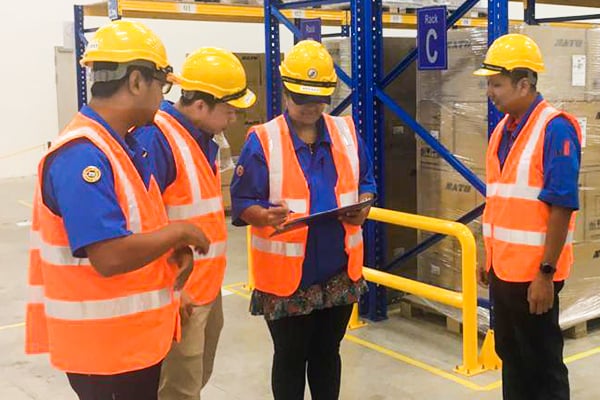
Annual fire drills
All employees participate in the annual evacuation drill.
Education and training
We have an external public agency train us on occupational safety and hygiene every year.
Hands-on practice prepares us for emergency situations.
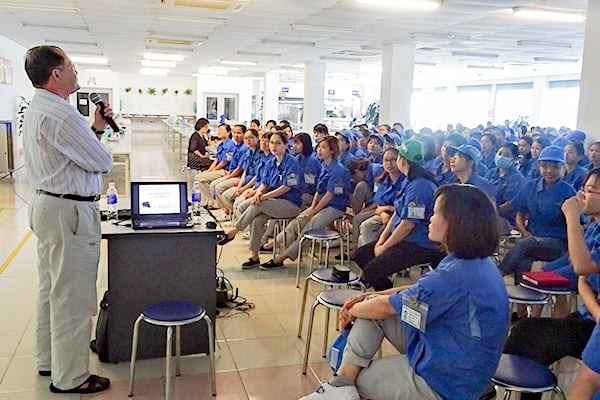
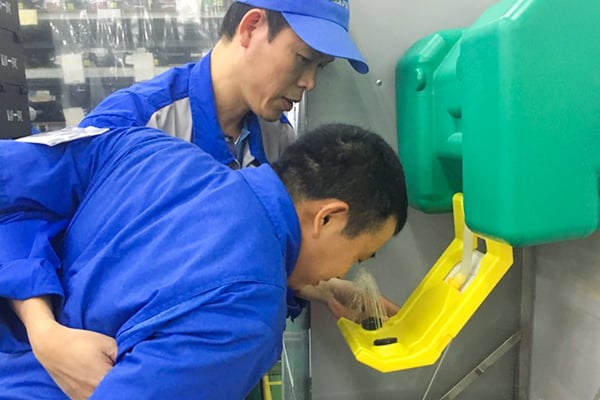
Employees suggest improvements
Teiho*, SATO's unique reporting system, allows employees to submit ideas and suggestions on how to improve safety and hygiene in our work environments. We find and counter risks and hazards, utilizing feedback from employees in every corner of our workplaces.
*A system for employees to submit and put into action original ideas, innovations and proposals to make the company better. Findings from customer feedback or market information are submitted to top management, and serve as a database for insight sharing.
Reporting occupational incidents
We draft detailed visualized reports on any occupational accident that occurs to be shared with all employees. We do this to eliminate the factors that caused the incident and to raise employee awareness on safety.
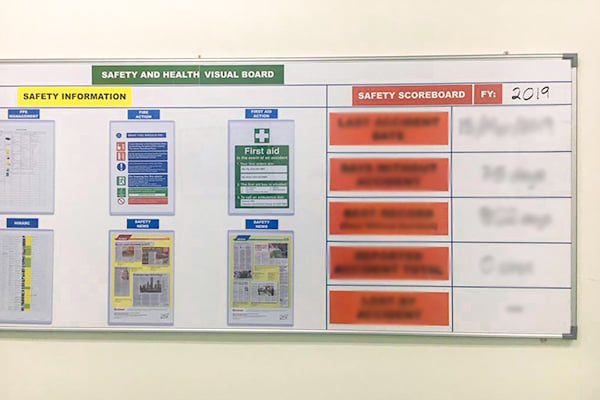
Employees' health and wellness
All of our factory workers are subject to annual health checks. We also partner with local medical institutions to seek immediate assistance at any time of the day in case of an emergency.