
Digitizing food production to deliver safety for all
What we do
Food production and food service require working environments where employees can provide safe foods in alignment with sustainable practices. Also, with the growth of cross-border e-commerce of food products, the need for traceability is growing as it directly affects the safety of consumers. Food traceability means connecting finished products on shelves all the way back to primary producers to earn the trust of consumers. Another subject of concern is food loss, exemplified by SDGs aiming to halve global food waste by 2030. This requires high accuracy in FIFO (first-in, first-out) rotation of ingredients. SATO helps operators across the food supply chain with solutions that use RFID. With RFID, food providers can know the correct inventory they need and purchase the right amount of ingredients.
Reassurance is at the heart of our “Right Food, Right Way” solutions. We help hotels, restaurants and caterers (HoReCa) ensure best practices with solutions for allergen labeling and FIFO expiry management. Traceability helps consumers make ethical food choices and it is a must for primary producers and food manufacturers.
We also support food manufacturers in their HACCP compliance efforts as they work to follow protocols at every step to grow their e-commerce import and export business. For the HoReCa industry, HACCP planning is crucial for operational excellence and food safety.
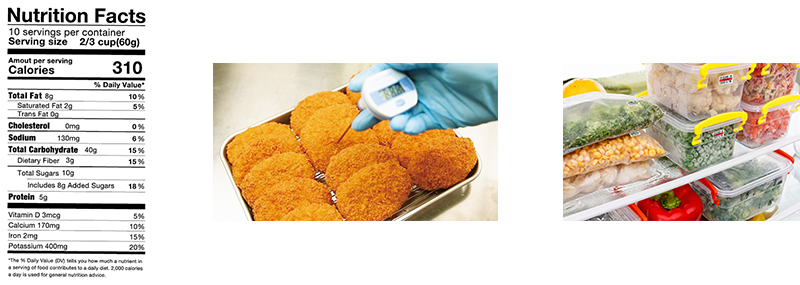
Solutions
- Allergen and ingredient labeling with FX3-LX and AEP apps
- HACCP compliance systems
- RFID traceability of food ingredients
Testimonials
- Ingredient labeling with brand uniformity for safety and assurance (EG Group)
- Central management of ingredient labeling data for efficiencies across outlets (SFBI (Asia Pacific) Pte Ltd.)
- Drastic productivity gains for food manufacturer through labeling automation (Otafuku Sauce Co., Ltd.)
- The right label in 1, 2, 3, clicks (Monte Pelmo)
Announcements
F&B manufacturers
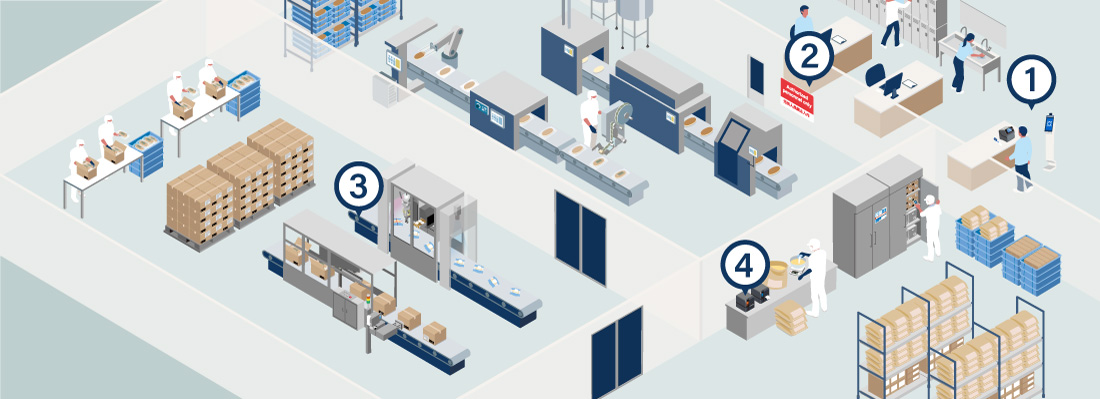
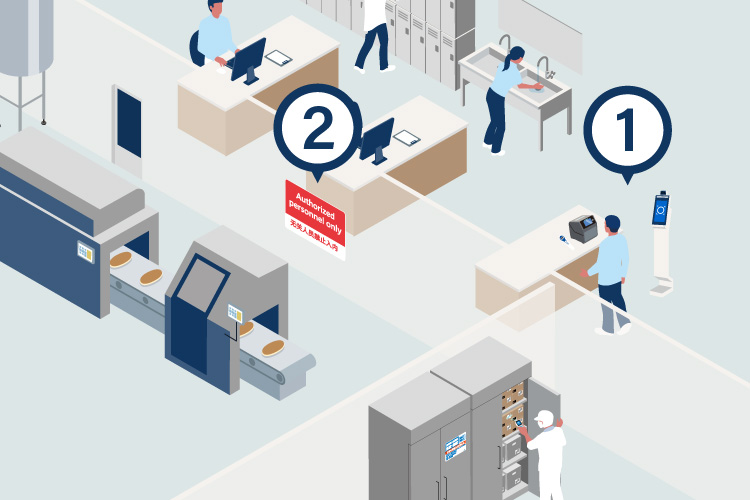
-
Implement contactless temperature check-ins with secure record-keeping.
Temperature check (for workplaces)
Challenges
- Thorough safety measures needed, starting from point of entry
- Temperature screening and data collection managed manually
- No real-time reporting of individuals with at-risk temperatures
-
Solution
Take and automatically store temperature readings for staff and visitors as they enter, issuing them with label-based entry passes if necessary.
- Detect symptoms to help reduce virus transmission
- Provide assurance with labels that can serve as proof of normal temperature
- *Not available in South America.
- *For other countries/regions, please contact your nearest SATO office to find out more.
-
Use stickers to promote practices that prevent infection.
Awareness-raising stickers
Challenges
- Inadequate safety precautions at workplaces
- Handwashing and other instructions not easy-to-understand for everyone
-
Solution
Put up stickers about infection prevention at highly visible areas such as entrances and restrooms to raise hygiene awareness in employees.
- Stickers to reinforce hygiene routines for a safe working environment
- Can be printed in standard layouts or designs original to customers
- Can also support images or texts in different languages to suit foreign workers
- *Availability varies by country/region. Please contact your nearest SATO office for more information.
-
Introduce automation to reduce close physical contact between workers.
Auto-labeling & packing
Challenges
- Workers at risk when performing labeling or packing in close proximity
- Possible production disruptions when workers are affected by the virus outbreak
- Lower productivity as factories seek to operate safely with less manpower
-
Solution
Automate label printing/applying and carton forming/sealing operations to keep fewer workers on site and distance them more effectively.
- Use automation to help protect labor force
- Ensure stable production even with manpower limitations
- *Availability varies by country/region. Please contact your nearest SATO office for more information.
-
Keep workers safely distanced and printer operations running stably.
Cloud-based support services
Challenges
- Cautious about admitting external technicians to sites due to virus fears
- Workers touch printers too often for configuration or troubleshooting errors
- No business continuity plan to sustain printer operations during emergencies
-
Solution
Oversee printer operations 24-7 via a cloud network to minimize errors/downtime and speed up recovery through preventative maintenance and remote support, reducing reliance on on-site servicing by outside engineers.
- Use an online maintenance service to monitor printers remotely and replace printer parts before they wear down to ensure worker safety and operational stability
- Also use a cloud-based data management service to always provide printers with the latest labeling data
- *Availability varies by country/region. Please contact your nearest SATO office for more information.
Food service operators (HoReCa)
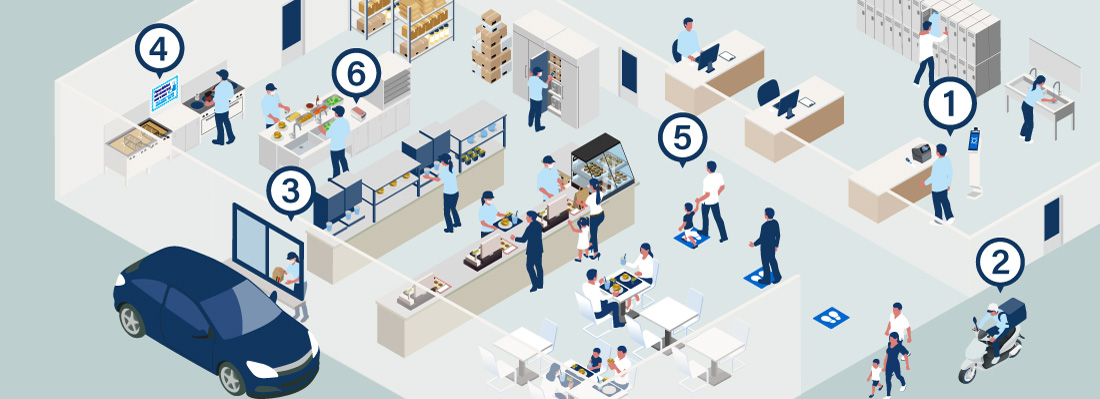
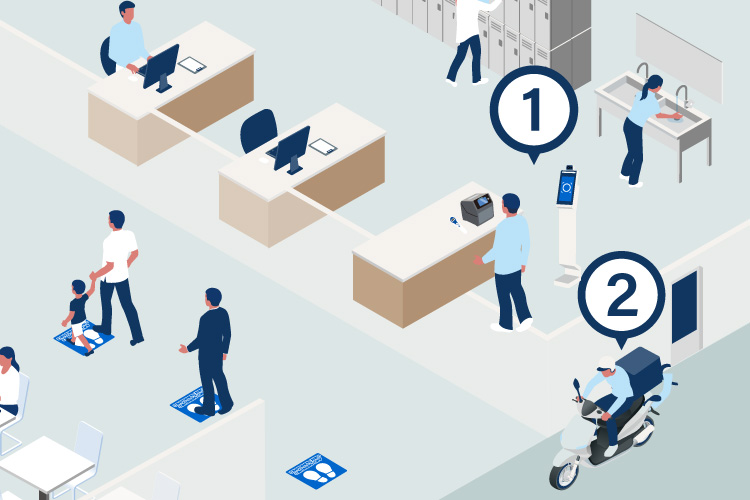
-
Implement contactless temperature check-ins with secure record-keeping.
Temperature check (for workplaces)
Challenges
- Thorough safety measures needed, starting from point of entry
- Temperature screening and data collection managed manually
- No real-time reporting of individuals with at-risk temperatures
-
Solution
Take and automatically store temperature readings for staff and visitors as they enter, issuing them with label-based entry passes if necessary.
- Detect symptoms to help reduce virus transmission
- Provide assurance with labels that can serve as proof of normal temperature
- *Not available in South America.
- *For other countries/regions, please contact your nearest SATO office to find out more.
-
Prepack deli/bakery items and label them individually for sale.
Tamper-evident labels
Challenges
- Reported cases of food pilfering by delivery drivers
- Customer concerns over the security and quality of their food orders
-
Solution
Provide reassurance that each order has remained untouched in transit via labels that separate into pieces to indicate tampering when peeled.
- Simple labels to prevent food tampering during delivery
- No changes needed to existing workflows and operations
- Can also be printed with timestamp, allergen, and other variable information
- *Availability varies by country/region. Please contact your nearest SATO office for more information.
-
Reduce food poisoning risks amid rise of takeout services.
Takeout labels
Challenges
- Rising attention on food safety as more eateries start offering takeouts
- Chances of takeout meals becoming contaminated when not consumed soon
-
Solution
Label takeout meals with the date and time the food is cooked to remind customers to eat them as soon as possible.
- Timestamp labels for the safe consumption of takeout foods
- Available in the form of hand labeler labels that can be used right away
- Can also be printed using label printers to indicate other information such as consume-by date and time (automatically calculated based on product master data)
- *Availability varies by country/region. Please contact your nearest SATO office for more information.
-
Use stickers to promote practices that prevent infection.
Awareness-raising stickers
Challenges
- Inadequate safety precautions at workplaces
- Handwashing and other instructions not easy-to-understand for everyone
-
Solution
Put up stickers about infection prevention at highly visible areas such as entrances and restrooms to raise hygiene awareness in employees.
- Stickers to reinforce hygiene routines for a safe working environment
- Can be printed in standard layouts or designs original to customers
- Can also support images or texts in different languages to suit foreign workers
- *Availability varies by country/region. Please contact your nearest SATO office for more information.
-
Use stickers to help customers practice safe distancing.
Floor marking
Challenges
- Inadequate safety precautions in stores
- Close proximity between customers, especially at checkouts
-
Solution
Clearly mark out distance required for social distancing to get customers in line without standing too close to one another.
- Floor stickers that can be rolled out quickly and easily
- Durable for use in high footfall areas
- Provide visual cues on where to queue for safe customer spacing
- *Availability varies by country/region. Please contact your nearest SATO office for more information.
-
Keep workers safely distanced and printer operations running stably.
Cloud-based support services
Challenges
- Cautious about admitting external technicians to sites due to virus fears
- Workers touch printers too often for configuration or troubleshooting errors
- No business continuity plan to sustain printer operations during emergencies
-
Solution
Oversee printer operations 24-7 via a cloud network to minimize errors/downtime and speed up recovery through preventative maintenance and remote support, reducing reliance on on-site servicing by outside engineers.
- Use an online maintenance service to monitor printers remotely and replace printer parts before they wear down to ensure worker safety and operational stability
- Also use a cloud-based data management service to always provide printers with the latest labeling data
- *Availability varies by country/region. Please contact your nearest SATO office for more information.
Find SATO where you are
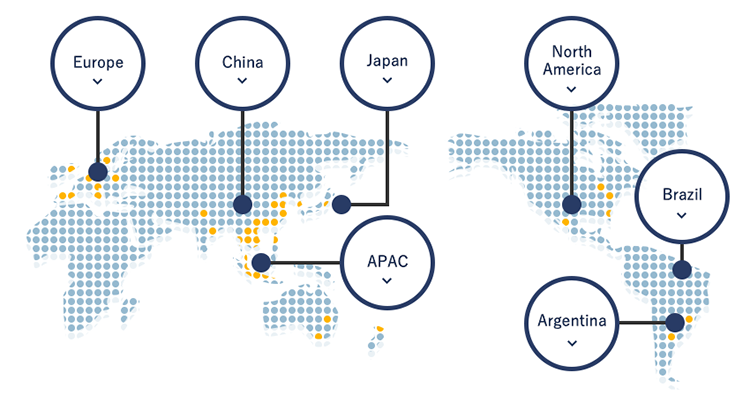
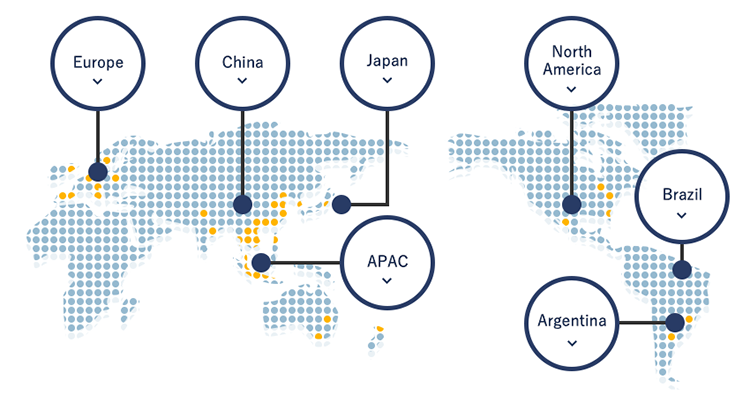